THE STORY OF RINGMAT
JOHN ROGERS REVEALS HOW HE AND DENIS
MORECROFT CONCEIVED AND DEVELOPED THE WORLD'S
PREMIER TURNTABLE MAT
Some years ago I had a call from a
gentleman in Holland; he was interested
in hearing a pair of Max Townshend's
Glastonbury speakers and as he was due
to visit relatives in England in a day
or so, could he call in and have an
audition? I was naturally delighted to
offer our hospitality and next morning I
started to set up a system for him to
listen to when he arrived.
At that time we had not had the speakers
for very long as they were then still
quite new to the market. We were very
impressed with their performance,
although up till then we had used only
modest equipment to drive them. So with
the forthcoming audition I decided to go
overboard to impress the customer,
wheeling out our Marantz CD12, Musical
Fidelity pre-amp and P270 power amp, and
wired up with our most expensive Van Den
Hul cables.
|
|
Recommended further
reading...
|
|
|
|
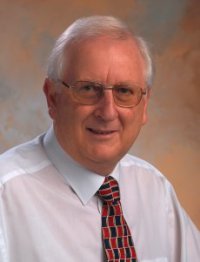 |
I switched on in anticipation of hearing
what I imagined would be heavenly bliss.
It sounded simply awful!!! I frantically
checked all I could think of, made this
adjustment and that, all to little
avail. So that afternoon I changed round
all the components, one at a time,
except the speakers. In the event, they
all had to go if the sound was to come
right, which eventually it did in all
its glory.
Over the months and years that followed,
I have been fascinated by the problems
of incompatibility between products and
the need to obtain the correct "loading"
in the system, so that an optimum match
is achieved between amplifier and
loudspeaker. I shall cover these matters
and the work I have done in connection
with them in another article at a later
date.
Some months after the Dutch visit,
having already worked out not only how
best to demonstrate the Glastonbury
speakers (successfully selling many
pairs) but to assess whether they were
best suited to a customer's system, I
prepared to demonstrate them to someone
who seemed to have a very suitable
system. I was pleased with the sound,
but as the customer had already
expressed a particular interest in
precise imaging, I spent some time
listening carefully in the "hot seat",
and could clearly discern what I thought
might trouble him. After a concentrated
period of experimentation, I found the
answer to the problem, which related to
the absolute phase of the recordings
used, phase changes in the signal chain
and the "orientation" of the drive units
in the speaker cabinets. I will also
deal with these subjects in a future
article, as they are endemic, in some
degree, to all hi-fi systems. See Hi-Fi
Advice –
Blueprint for the Future
|
The reason I mention all these earlier
experiences is that they prepared me for the
beginning of a long journey on which I am still
travelling - namely, to determine the means by
which it is possible to recreate on playback a
quality of reproduction which, as nearly as
possible, reproduces in the listening room the
original performance that was recorded (given
the sometimes limited quality of the recording
itself). I hope that this and subsequent
articles will provoke interest in what I regard
as fundamental problems in the hi-fi industry
and why it has been failing its customers - the
public.
The issues raised above, which I shall
be discussing more fully in later
articles under Hi-Fi Advice – Blueprint
for the Future, have had an enormous
impact on our business. Not only did
they govern the way we looked after our
customers when our business was largely
retail, they also provided the impetus
we needed to devote more time and
resources to research work and to the
design, manufacture and marketing of our
own products. This impetus stemmed
primarily from our frustration in retail
when we found that not all the
components needed for the standard of
reproduction we were seeking for our
customers were available.
In designing each product, we have
inevitably drawn on our experience in
retail and the special insights that
have been gained in recent years by
myself and my colleagues in the way
components work and in the way the
signal is handled by those components.
In particular, we have concentrated on
how electrical and mechanical vibrations
at the front-end of the system, where
the signal on playback is first
generated, affect the phase of the
signal that is heard as sound from the
speakers. As a result, each product is
somewhat unique in the way it tackles
problems of reproduction. RINGMAT was
the first of these products to be widely
marketed and is the standard to which
all our products will, in future,
adhere. Because of this, I shall explain
the function of RINGMAT, its importance
in helping to reproduce a clear signal
and, more importantly, an accurate
signal, and how it was developed; and
later, how it evolved into an even
better product.
|
 |
RINGMAT was a joint development between
Denis Morecroft of DNM Design and
myself, representing QR Design, the
design arm of our business. The basic
idea was initially Denis Morecroft ‘s,
and I became
involved at a stage when I had already done much
of the research work mentioned earlier in this
article, some of which I had discussed with
Denis. The collaboration was also brought about
by the fact that, when in retail, we stocked the
DNM amplifiers and solid core cable, and had
jointly held some "musical evenings" for our
customers; and we both lived and worked in the
Brentwood area. Denis was developing a DNM
turntable to be called the "Rota", which was to
be marketed with the amps, cabling and the
French made Rehdeko speakers that were
distributed alongside the DNM products, making a
complete vinyl system. For the new turntable to
be an advance on what was already on the market,
it had to deal more effectively with those
adverse influences that usually inhibited the
reproduction of a clear signal.

Denis
Morecroft
|
As readers will be aware, there are many
approaches to turntable design, but in
general they fall into two schools of
thought. Each endeavours to overcome the
vibration problems caused by unwanted
energy from both the tracing stylus and
the sound pressure waves in the room, as
well as any inbuilt vibrations from the
working of the turntable itself. The
unwanted energy causes the stylus to
move in a way that is unrelated to the
original signal and the accuracy of
reproduction is reduced accordingly. One
approach towards overcoming this problem
is to try to simulate the conditions
under which the record was originally
cut by clamping the record to a solid,
heavy surface which will hold it still,
prevent any movement and therefore allow
so-called "perfect" reproduction of the
information in the record grooves.
Another method is to allow movement to
occur but to arrange it so that it is as
inaudible as possible.
The first of these two methods is not
ideal because it is impossible to
exclude all vibrational energy in any
material; in practice, the energy will
always be changed in form or reflected
back into the system from which it
originated. The second method is more
practical, but hitherto it had not been
properly designed in a "total system"
approach. Denis wanted to make a
turntable that was quite different, as
is always the case with him, by
incorporating many innovative ideas, the
most outstanding and recurring feature
being the decoupling of certain elements
in a way that enabled the stylus to
track the record as free from inbuilt
and room resonance's as possible. |
As the interface between the vinyl
record and the platter would naturally
play a crucial part in this overall
concept, one of the first design
initiatives was to find a new way to
support the record on the platter. Denis
believed that none of the previous
approaches to this problem had
satisfactorily resolved the matter and
was looking at new ways of solving the
puzzle. He conceived that the record
must be supported in a manner that
allowed movement but, as far as
possible, such movement had to be
outside the audio band. Any movement
that occurs should be as free as
possible from structural resonance's
within the record itself or anything
attached to it, including the surface on
which the record lay e.g. its support
mat. The record support mat must
generate the minimum noise whilst
absorbing the movement and dissipating
the unwanted energy. Essentially, there
was to be minimal contact with the
underside of the record and as much air
as possible between the playing surface
of the underside of the record and any
structure designed to support the record
on the platter. |
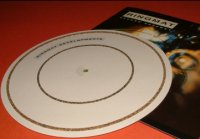 |
Using
his then resident Linn LP12, Denis showed me
what happened if, for example, the record was
supported only at the centre (under the area of
the label) by a thick mat of soft felt. I was
immediately struck by the increased clarity,
openness and fullness of the sound. However, I
was concerned with the way the record "flapped"
a bit because of the softness of the felt, and
in any case, I was not a lover of felt mats
because of the noise they generated through
friction under the record. I said I had a few
ideas we could try and would experiment back at
our own premises.
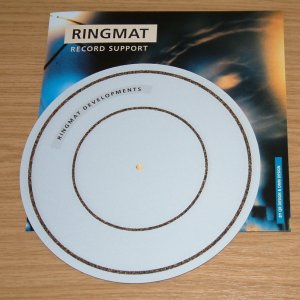 |
My first decision was to find a
replacement for the felt. I knew Mike
Knowles at Alphason had taken a great
deal of care in developing the surface
they used for the platter of the Sonata
turntable, where the record rested
directly on the platter. As it was not
practicable to use his materials, I went
for what I considered was the nearest
equivalent - cork. I also liked this
material because of its properties in
relation to aspects such as static.
Many types of cork were tried and all
were found to be far superior to the
felt. It was also found that significant
variations arose according to the size
and shape of the cork used and its
placement under the record, and that, by
restricting the contact area,
considerable improvements in sound
quality were obtained. This led to the
development of the cork rings. However,
we were achieving different results from
the various types of cork and found that
one type was best for contact with the
record itself whereas another was better
on contact with the platter underneath.
I then decided it was time to experiment
by building into the structure a degree
of movement, such as we earlier had with
the felt, only more controlled. This
eventually led to the development of
rings on a substrate but we were having
difficulty in finding something suitable
for the substrate that provided the
right speed of movement and control.
Eventually we found a paper that
incorporated cotton and cotton flock,
which provided just the right degree of
movement, as well as minimising
resonance. The structure also had plenty
of air between the underside of the LP
and the substrate and between the
substrate and the platter. The
significance of this was that the
enormous energy generated by the stylus
as it tracked the groove of the record
could readily be dumped into the air
above and below the substrate. With hard
mats like rubber, and with bare platters
such as acrylic and glass, and even with
the special textured surfaces like the
Alphason, this energy is reflected up
the cantilever and comes out of the
speakers as distortion. The effect is
similar with felt mats, though to a
lesser extent because there is some
"give", but there is the added problem,
to which I have already referred, of
noise caused by friction between the mat
and the record. |
At each stage, both Denis and I were carefully
evaluating the progress made by means of
listening tests. Also, Denis was meanwhile
obtaining computer printouts of resonances of a
standard 12" record and from this data we placed
cork rings at the various significant points
during the listening tests. It soon became
obvious where the main support ring should be
placed for the primary support of the record -
in the middle of its mass.
Thus we arrived at a construction whereby the
record had minimal contact with its support mat.
It rested on a main ring under the centre of its
mass and, via the special paper substrate, this
main ring moved between two rings on the
underside. The mat also provided a good
impedance match for transferring unwanted
vibration energy into its own structure and
effectively dissipating it into the air
underneath the record and its support mat. The
minimal contact with both record and platter
surface also meant that very little noise was
created underneath the record by reason of
contact movement. To improve the resonant
properties of the mat and its impedance
matching, the mat also benefited from a second
ring placed nearer the centre, which we found
had to go on top of the substrate, though we
would have preferred some support below it; this
aspect featured as a further development of the
mat in a later model. We affixed the logo, and
RINGMAT 330 was born in the late Autumn of 1992,
after some 18 months of joint development work.
The attractiveness of the product was
that it could also be used on almost any
turntable with equally beneficial
results, irrespective as to whether the
turntable was inexpensive or in the
super league, or whether it was of high
or low mass, or whether or not it had a
suspended sub-chassis. For obvious
reasons, it could not be used on those
platters using suction devices, or those
that had a significant "dishing" effect.
Those that had felt or some other
substance stuck to the surface of the
platter generally needed to have it
removed in order to obtain the best
results.
I was, however, concerned that some of
the less expensive turntables that had
fixed height tonearms may have
difficulty in coping with the thickness
of the mat at around 3mm, so RINGMAT
models 200 and 250 were created with
thinner paper and, in the case of the
200, with the top rings having a lower
profile to reduce the overall thickness
of those mats; model 250 lifted the
record about 2.4mm off the platter and
model 200 about 1.8mm. However, the
thinner paper was not quite as ideal as
that used for the 330, so although the
difference in performance was small, the
330 definitely had an edge.
How would one describe RINGMAT? Well, it
is a unique (patented) design, which
enables 12" records to be supported so
that the main vibrational modes of
record movement - caused by input of
stylus energy - give the minimum
possible error signal. It can also be
used with vinyl records of other
diameters with some success and works
extremely well with 78s. |
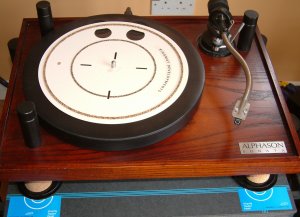 |
I believe it is the first time that such a
component has been properly designed. Its use
has also eliminated or reduced many of the
problems associated with record reproduction,
many of which have, in the past, often been
wrongly blamed on other parts of the hi-fi
system, especially the speakers.
With RINGMAT, there is a reduction in background
noise, with a cleaner, crisper and yet more
delicate sound. It brings greater resolution and
separation to the sound, together with a wider
and deeper soundstage; there is an enhanced
sense of power, with greater weight and
authority in the bass. Some of these attributes
may be difficult to realise in practice. There
are numerous reasons for this, which are related
to problems elsewhere in the hi-fi system; some
of these will be discussed in future articles.
See Hi-Fi Advice –
Blueprint for the Future.
In the Autumn of 1994, a MkII version of the 330
was launched which contained that inner ring
under the substrate that we had previously found
so difficult to place. The newer version also
used a slightly different mix of the paper
constituents and contained a small plastic
sticker near the spindle hole; how we came by
this is an interesting tale. I accidentally tore
the paper of one of the RINGMAT 330s I was using
for development work, but rather than throw it
away I put a piece of Sellotape over the tear
and put the 330 to one side. Some weeks later,
after significant improvements towards the new
MkII version, I went back to the torn 330 to use
as a benchmark - I was both astounded and
puzzled that in certain aspects it was better
than anything I had developed thus far and could
not at that time work out why. I checked this
and that, and was nearly tearing my hair out
when it occurred to me that the piece of
Sellotape was having a significant effect.
Indeed it was, as simulated stickers of various
shapes and sizes placed in various positions
testified. It became clear that, whilst the logo
was having a beneficial effect on the resonance
of the mat itself and its impedance matching, it
needed to be "balanced" and the sticker, as now
used, does just that.
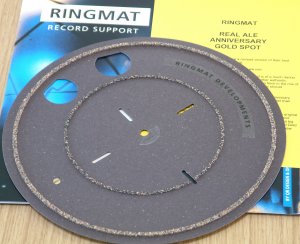
Ringmat
Real Ale Anniversary Gold Spot |
Also, for some time, I had been
concerned that with most records the
area around the label was of a greater
thickness than over the record as a
whole and I felt this may not have been
taken sufficiently into account in the
computer analysis we did. I was also
interested in the effect that very small
variations in the width and spacing of
the rings had on the sound and after
long periods of experimentation and
evaluation I finally settled on a
formula that gave a significant and
worthwhile improvement in the sound,
mainly in the way the stylus was now
able to track the groove with even
greater security, enabling not only the
bass but all frequencies to drop lower
and much nearer to their natural level,
thus enabling the system to obtain a
much greater degree of drive and power
to the sound. Another benefit of the
slightly wider top ring we adopted was
that the inner top ring could now be
reduced in profile. All these
improvements were incorporated in the
new RINGMAT 330 MkII XLR launched in the
Spring of 1996.
In the Autumn of 2001 we celebrated 10
years of Ringmat design with the
introduction of the first new Ringmat
since the XLR in 1996, the Anniversary
Ringmat. This new Ringmat had certain of
the anti-resonance cut-outs to be found
in the Ringmat Spacers and an
improvement in the operation of the
rings through the use of a different
type of adhesive between the cork rings
and the paper substrate.
With our other Ringmats,
the rubber-based adhesive included a
polyester carrier, which acted as an
interface between the cork rings and the
special paper substrate. With the
Anniversary, the acrylic adhesive does
not involve a carrier and a more direct
contact is made between the cork rings
and the |
special paper. This creates a more immediate
sense of presence in the sound and a much
stronger bond between the paper and the cork
rings.
The anti-resonance “cut-outs” improves the
dynamics of LP sound reproduction; the amount of
information retrieved is greater and this also
helps create a much larger, wider sound stage.
This is particularly impressive when the
ANNIVERSARY RINGMAT is used as part of the
RINGMAT SUPPORT SYSTEM. In this instance, we
suggest the “cut-outs” in the ANNIVERSARY
RINGMAT are aligned with the direction of the
“cut-outs” in the Spacers, with the LP STATMAT
and RINGCAP also following the pattern. Because
the individual components are of a different
size, the “cut-outs” do not directly overlay
each other, but the general layout and
direction, based on the position of the Spacers,
will be clear.
It may now be an appropriate time the write more
about the “cut-outs” in the Anniversary Ringmat
and also many other Ringmat Products, such as
the Ringmat Spacers, Ringmat Base Platter Mat,
Ringmat CD and LP Statmats, Statfeet, and the
Ringmat Vivacity Sparkle Sheet. This is because
it involved a study in the use the earlier
Ringmats on turntable platters that had holes to
enable a manual change to be made in the
turntable speed by moving the turntable belt
from one drive to another using fingers through
the holes on the turntable platter. In order to
establish whether the holes in the platter had a
detrimental effect on the use of a Ringmat, a
trial was carried out. This established that the
presence of such holes actually had a beneficial
effect, rather than a detrimental one, even if
the holes were introduced in a piece of material
laid on top of a platter without the holes.
Further evaluation demonstrated that the
relative sizes of the holes was critical, as was
the distance between them and where they were
positioned relative to the mass of the platter.
After a great deal of further study, we
discovered a geometric model whereby the
removal, and/or addition, of mass at certain
critical points of a piece of rigid flat
material radically improved the outcome as
regards the quality of sound reproduction due to
a reduction of resonance in the flat material,
and that it was not restricted to situations
where a turntable was involved. Not only round
holes, but other shapes and sizes, but their
actual sizes, shapes and positions had to be
precise and any slight deviation outside a
certain tolerance nullified their beneficial
use. Additions to mass also include the use of
adhesives and stickers. In the case of our
Ringmat Vivacity Anti-Resonance Platforms, our
use of both the NXT patented Distributed Mode
Loudspeaker technology and our own modelling
regarding the beneficial effects of a reduction
and/or addition of mass to flat materials has
resulted in stunning results in the field of
sound reproduction, as well as the other Ringmat
products mentioned above.
By extension, such a reduction and/or addition
to mass in order to reduce resonance probably
has applications in other fields of activity,
not only to the use of rigid flat materials but
also other forms of material, such as sheets of
material that are not necessarily used flat.
Nearly six years later, in August 2007, we
introduced the Anniversary Gold Spot Ringmat.
Here we introduced a more advanced, and thinner,
adhesive, thereby further reducing the layers of
substance between the cork rings and the paper
substrate to provide an even more “immediate
sound” when playing LPs. We also introduced a
new concept in sound technology in the design
and manufacture of the “Gold Spot” itself, which
has incredible beneficial results in sound
reproduction. Initially, it is being used just
for the Anniversary Ringmat, but in due course
it will be used with other Ringmat products.
In 2012, we were delighted to announce a revised
version of our best selling Anniversary Gold
Spot Ringmat called the “Real Ale” version. This
primarily involved a change in the paper we
used, to one containing beer grains instead of
cotton. This happily occurred because the paper
we had been using from the very beginning of
Ringmat suddenly no longer became available due
to the closure of the paper manufacturer we had
been using – we say “happily”, because when it
happened there was great concern whether we
could find an alternative paper that would
provide a level of performance to that which we
had enjoyed for many years; in the event, the
“Real Ale” paper was even better for making
Ringmats, but it was thicker and therefore could
not so easily be used for the thinner Ringmats,
especially as the thinner paper that had been
used for the Ringmat 200 and 250 was also no
longer available.
Fortunately, we still have some stocks of the
original Anniversary Ringmat paper and also
stocks of the same Ringmat paper but in a
blue/grey colour instead of the buff coloured
paper we had been using. The blue/grey paper is
slightly thinner than the buff coloured paper
(by about 0.030mm) and will in future be used
for the Ringmat 330 MkII XLR; also for the
Ringmat 200 (which will now be 2.4mm thick) and
the Ringmat 250 (which will now be about 3mm
thick). If we come across suitable thinner paper
to enable us to make thinner 200s and 250s, we
will do so. Once adjustment has been made for
the very slight reduction in thickness of the
blue/grey paper, the sound of the XLR is
identical to that in recent years using the
earlier buff coloured paper, whilst the
performance of the new Ringmat 200s and 250s is
greatly improved, not only by the use of the
better quality paper but also because of the use
of a better and thinner acrylic adhesive. So all
round, the quality of the Ringmat range has now
vastly improved.
Some people have asked whether RINGMAT can be
used with a clamp. Whilst this may physically be
possible, it is undesirable for the way it often
"shuts in" the sound and changes all the
parameters that are so beneficial in the RINGMAT
as it stands. (Please bear in mind that the
Ringmat is only one part of the Ringmat Support
system – there is also the Ringcap and many
other parts to complete the best support system
available for an LP record). The benefit of
RINGMAT is that it works with the natural
resonance's that are being created and dumps
them into the air, whereas clamping stresses the
record, changes the nature of the resonance's
and reflects them into the signal chain; as the
record itself comes under stress, it acts like a
bell - and what happens when a bell is struck?!! |